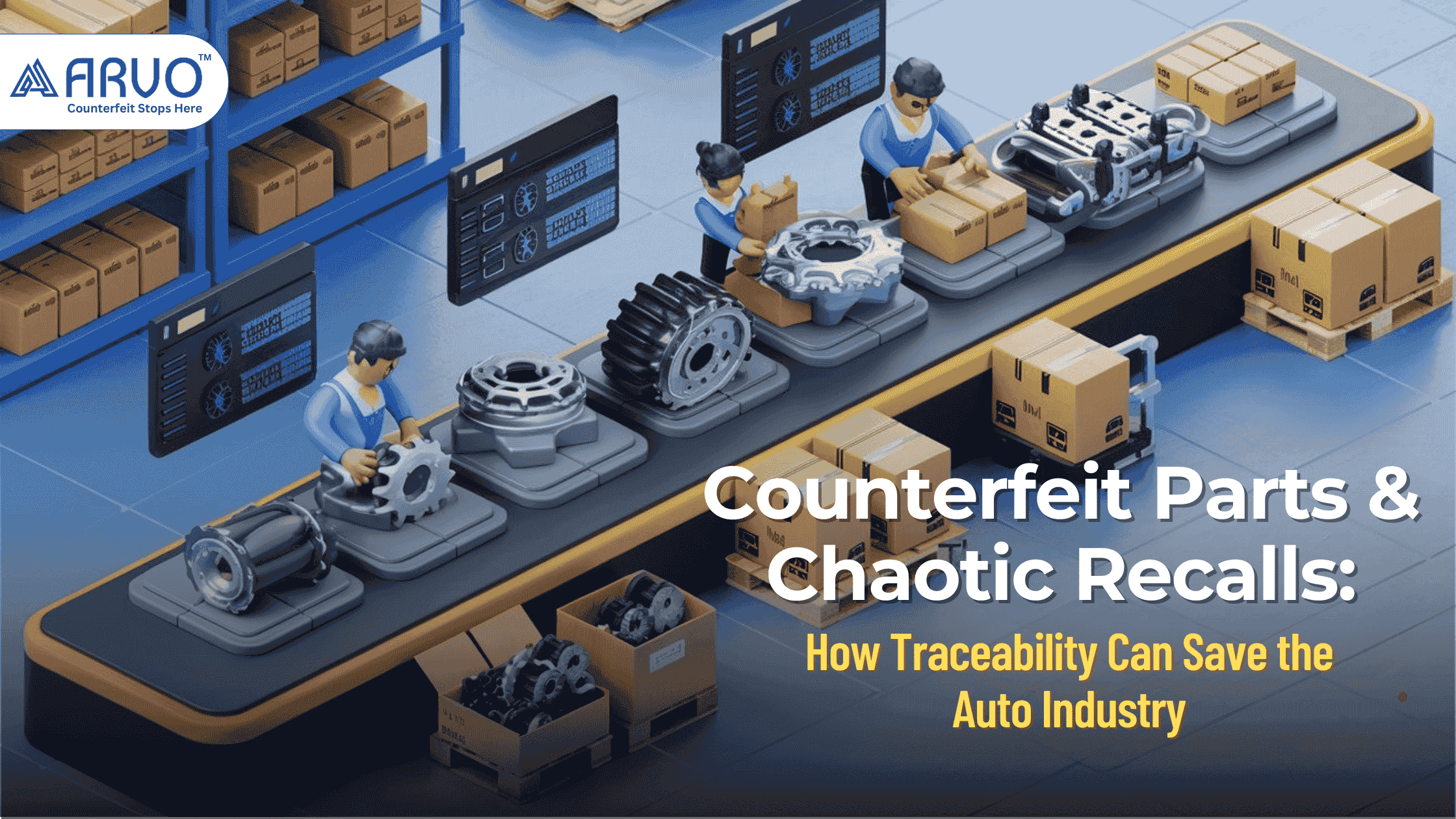
Every year, thousands of dollars are lost, reputations are tarnished, and lives are endangered because of one critical weakness in the automotive industry: the lack of supply chain traceability. Counterfeit parts infiltrate systems undetected, recalls become chaotic and costly, and regulatory pressures mount—all because of blind spots in a process meant to ensure quality and safety. For auto parts manufacturers, the stakes couldn’t be higher: without traceability, the entire industry is at risk of collapse under the weight of inefficiency, non-compliance, and trust deficits.
The global automotive industry is a vast, interconnected network. As vehicles become more sophisticated, so do the components that make them. Auto parts travel across continents, passing through numerous suppliers, manufacturers, and distributors before reaching the end consumer. However, this complexity brings significant challenges, particularly regarding traceability.
For many manufacturers, maintaining end-to-end visibility is an ongoing struggle. These “supply chain blind spots” can lead to counterfeit risks, compliance failures, costly recalls, and loss of trust. Despite the importance of traceability, many auto parts manufacturers lack the tools and systems to track parts effectively.
The Growing Problem of Traceability Gaps
Failing to trace components accurately in the fast-paced automotive industry can have far-reaching consequences. Here are some of the most pressing issues:
1. The Rise of Counterfeit Auto Parts
Counterfeit auto parts are a $45 billion global problem, according to industry estimates. Fake parts infiltrate supply chains undetected, compromising vehicle safety and performance. These counterfeits often look identical to genuine components but fail to meet the necessary quality and safety standards.
When counterfeit parts reach consumers, the consequences can be catastrophic:
- Safety Hazards: Substandard parts can lead to vehicle malfunctions, accidents, and fatalities.
- Reputational Damage: Manufacturers may be blamed for failures caused by counterfeit parts, eroding trust with customers.
- Financial Losses: Addressing counterfeit-related issues, including recalls and lawsuits, can cost millions.
2. Increasing Supply Chain Complexity
Modern supply chains are incredibly intricate. A single vehicle may contain parts from dozens of suppliers across multiple countries. This complexity creates opportunities for errors, miscommunication, and inefficiencies, such as:
- Missing or incomplete data about the origin of parts.
- Difficulty tracking components through multiple stages of production.
- Inability to verify the authenticity of parts at various checkpoints.
3. Inefficient Recall Processes
Recalls are a fact of life in the automotive industry, but without effective traceability, they become unnecessarily expensive and time-consuming. Manufacturers often struggle to:
- Identify affected parts quickly.
- Isolate defective components without disrupting the entire supply chain.
- Notify stakeholders and customers on time.
In the absence of proper tracking, manufacturers may be forced to overcompensate by recalling more products than necessary, resulting in wasted resources and damaged reputations.
4. Growing Regulatory Pressure
Governments and industry bodies are implementing stricter government regulations to ensure product safety and transparency. From material sourcing to end-of-life disposal, manufacturers are required to provide detailed documentation for every component. Failing to comply can lead to penalties, delays, and loss of market access.
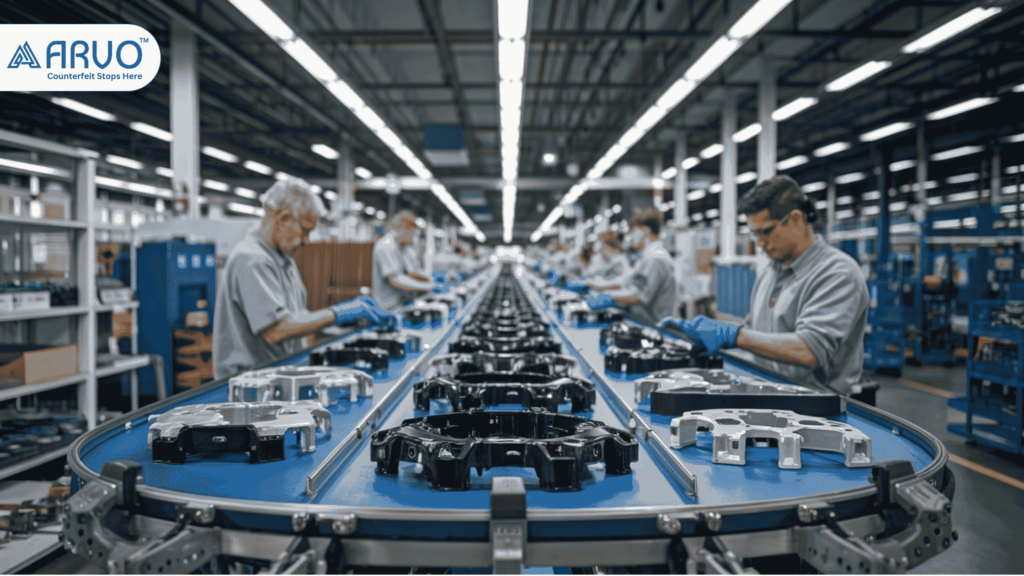
Root Causes of the Traceability Problem
Why do so many auto parts manufacturers struggle with traceability? The issue often stems from outdated practices and a lack of technological integration:
- Manual Processes: Many manufacturers still rely on paper records, spreadsheets, or legacy systems that cannot handle the demands of modern supply chains.
- Siloed Data: Information is often scattered across different departments and systems, making it difficult to consolidate and analyze.
- Limited Investment in Technology: Implementing advanced traceability solutions requires upfront investment, which some companies hesitate to make despite the long-term benefits.
The Impact of Supply Chain Blind Spots
The lack of traceability isn’t just an operational challenge—it’s a business risk. Here’s what manufacturers stand to lose:
- Customer Trust: Consumers expect transparency and assurance that the parts in their vehicles are authentic and safe. Failing to meet these expectations can drive customers to competitors.
- Operational Efficiency: Blind spots lead to inefficiencies, such as production delays, inventory mismanagement, and increased costs.
- Competitive Edge: In a market where traceability is becoming a key differentiator, manufacturers without robust solutions risk falling behind.
How ARVO’s Traceability Solutions Close the Gaps
Traceability solutions are the answer to these challenges, enabling manufacturers to regain control of their supply chains and eliminate blind spots. Here’s how:
1. Copy-Proof QR Codes
These secure QR codes are designed to be tamper-evident and impossible to replicate. They allow manufacturers to authenticate parts at every stage of the supply chain, ensuring only genuine components are delivered to customers.
2. Serialized QR Codes
Serialized QR codes assign unique identifiers to each product. This makes it possible to track individual parts throughout their lifecycle, from production to delivery, enabling precise recalls and quality assurance.
3. NFC Labels for Real-Time Verification
Near Field Communication (NFC) labels provide a seamless way to verify authenticity. With a simple scan, stakeholders can access real-time data about a product’s origin, journey, and compliance status.
👉 Contact us today to discover how Arvo can help your business achieve complete supply chain transparency and eliminate blind spots. Let’s build a smarter, more secure future together!
Conclusion
The automotive supply chain’s complexity makes traceability more critical than ever. Without the right solutions, manufacturers risk financial losses, regulatory penalties, and reputational damage. By adopting advanced technologies like copy-proof QR codes, serialized QR codes, and NFC labels, companies can eliminate supply chain blind spots, protect their brands, and build trust with customers.
FAQs
1. What is traceability in the auto parts industry?
Traceability means the ability to track a component’s journey through the supply chain, ensuring transparency and accountability at every stage.
2. How do QR codes improve traceability?
QR codes store and provide access to detailed product information. Copy-proof and serialized QR codes ensure authenticity and precise tracking for every part.
3. What makes NFC labels ideal for supply chain tracking?
NFC labels enable instant data access with a simple scan, providing real-time information about a product’s authenticity and movement.
4. Why is traceability essential for recalls?
Traceability allows manufacturers to identify affected components quickly, minimizing recall costs and ensuring consumer safety.
5. Can traceability solutions prevent counterfeit parts?
Yes, technologies like copy-proof QR codes and NFC labels help detect and eliminate counterfeit parts before they enter the market.
6. How can manufacturers start improving traceability?
Start by integrating technologies like copy-proof QR codes, serialized QR codes, and NFC labels into your supply chain to ensure end-to-end transparency and security.